Beech 18 Spar Replacement
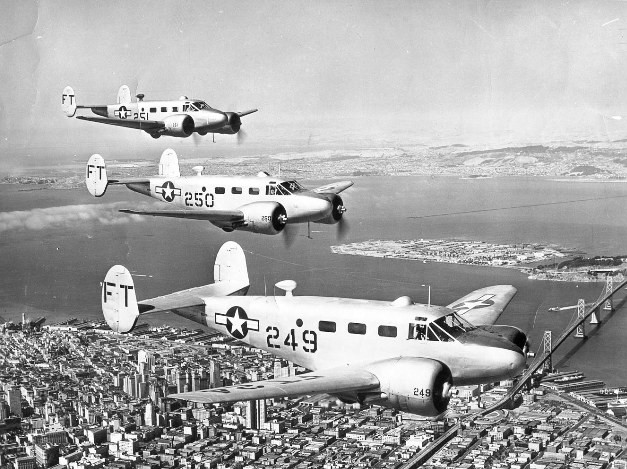
The following is a response to an email sent, which details the process for replacing the spar.
"Hello Mark
Funny you should ask, but I am in the middle of replacing a spar in an AT-11. The spar had internal rust which breached the lower elliptical tube about 8 inched from the fuselage. This aircraft was a special case because it had an Air Force mod that drilled holes in the spar for a reinforcement thus opening the inside of the spar to the atmosphere.
To the owners credit, he has decided to replace the entire truss instead of scrapping the historic AT-11. He puts a high value on saving this great Warbird when most others simply would have walked away.
I found a TC-45H that had been cut up to use as a spar donor and we removed the truss. Instead of chopping the spar out of the TC-45H I had my crew carefully remove the spar as practice for doing the same on my customers AT-11. Before we began I collected as many factory photos that I could find to try and learn how the aircraft was built. Indeed the aircraft was built around the spar with sub assemblies coming together around the spar which was fixed in the jig.
I am fortunate to have a young kid working for me who has taken a personal interest in this project. You know the kind of personality that I am talking about; the kid who wakes up in the middle of the night with a revelation about how to solve a problem...I am fortunate to have Steve working for me. I have put him in the lead position on this huge project and he is flying high.
Since the aircraft was assembled around the spar we needed to figure out how to do as little disassembly as possible and yet gain complete access to the spar.
You need to remove the following components: Flaps and wings; Fuel and oil tanks; and disconnect all of the controls and plumbing to the firewall.
You can drill off the firewall and the complete nacelle structure in one piece
De-skin the leading edges between the nacelle and the fuselage. between this and the nacelle removal you can now get to the plumbing and controls a lot easier.
Remove all of the controls and plumbing that runs through the truss. If you must, you can leave it connected to the control pedestal and instrument panel but for the restoration I am sure you will completely remove these components for individual restoration and rework.The floor structure of the cockpit mounts to bulkhead 5 (aft of the cockpit seats) through the spar truss so it needs to be removed. The skins surrounding the spar need to be removed so the easiest way to get access with minimal disassembly is to de-mate the nose from the fuselage at bulkhead 5. The roof of the cockpit stays with the fuselage and the rest of the cockpit comes forward and off with the assistance of a forklift (or 4 people).
At this point there are many other structural members that need to be removed but pay careful attention to the sequence because if you drill off the wrong rivets you may have to do further disassembly just to be able to put things back together. I will put together a web page with the photos of the sequence as we have taken over a thousand digital pictures so far.
With the nose removed and the spar completely exposed it is time to do some severe measuring. We built a solid frame that supported remaining structure after the gear was removed. It was easy to secure the AT-11 fuselage as we just bolted onto the aft outboard bomb door hinge holes and the mount plate for the 30 cal machine gun in the tunnel opening. We built the three point frame with fine threaded rod so we could level out the fuselage.
With the fuselage leveled we dropped plumb bobs on the center line of the fuselage at the center of the spar and the center of the tail. We marked these pin points and then snapped a chalk line on the floor. We then dropped two plumb bobs one at each upper wing attach over a wing pin and down the vertical truss tube. We them measured from these points to the center line and to the tail. I wanted to see just how straight the truss was in the fuselage and to my amazement after 60+ years the dimension from the wing attach to the center of the tail was within 1/32 of an inch! Well done Beech.
There was a slight twist to the fuselage at the horizontal stabilizer attach of 1/16 of an inch but I think we can take care of that when it comes time to install the horizontal.
With the measurements done it is time to drill off and un bolt the spar from the fuselage and wing stubs. It is necessary to cut the drag tube that extends from the middle of the spar to the fuselage at the trailing edge. You can completely disassemble the rest of the wing stub to try and take this apart intact but it is simpler to cut the tube. There is a factory procedure for replacing the spar truss from the fuselage out and it details cutting this tube and the splice to put it back together. With this factory documented data and how it will make later alignment easier cutting the drag tube is the best way to go. Incidentally the inside of this tube was in good shape with slight surface rust beginning but you can see that the linseed oil had drained to the bottom of the tube and looks like a black stripe.
It was interesting to uncover the pencil and grease pencil markings and notes that the workers made on the structure at the factory. We used special plates bolted to the jack pads mounting lugs so the truss could be supported by jacks. The jacks on casters made it possible for the truss to roll forward off of the fuselage with several well placed jerks...me being the biggest jerk in the shop...
We are now cleaning up the truss and are contemplating the finish coat for the spar. I am researching powder coating the truss with a MIL SPEC process that seems to be bullet proof for accelerated age tests. I am concerned about the 375 degree temperature and the metallurgy of heat treated 4130. More research required. I am trying to talk the owner into a copper plated base coat with a polished nickel plate on the spar...just kidding! I bet I will have a customer in the future who will want a chrome plated spar.
I intend to come up with a method of internal preservation for all of the tubes in the truss as the linseed oil sitting on the bottom of the open drag tube is a great indication of what all of our trusses will look like. I am going to use the rusted spar for developing an efficient method of preservation.
The project continues...it is easy to tear things apart but the proof is in the replacement. We can get the new spar in soon but we are going to take this opportunity to clean, repair and paint the nose and open fuselage structure before it is replaced.
Mark, your comments about removing the spar because you are a perfectionist are completely justified to me. I understand how you feel and I applaud your attitude. You should come and visit us to see what we are doing as it will reduce your learning curve dramatically. It is very hard to gain access to clean a spar entirely without removing it but we have done that on the other AT-11 in our shop. Come on by and take a look.
It took two guys about 5 days to get the parts removed from inside the fuselage and wing stubs. It took them another three days to get all of the sheet metal off. three more days for nose removal, measurements and to have the spar on the floor. Having been through the initial learning curve on the spar removal I think we can do it quicker the next time. As I mentioned earlier the big job lies ahead, getting the spar back in with clean sheet metal work that exceeds the quality at the factory will be the challenge. Fitting the D model spar into the C model aircraft presents its own challenges.
Stay tuned,
Taigh Ramey"